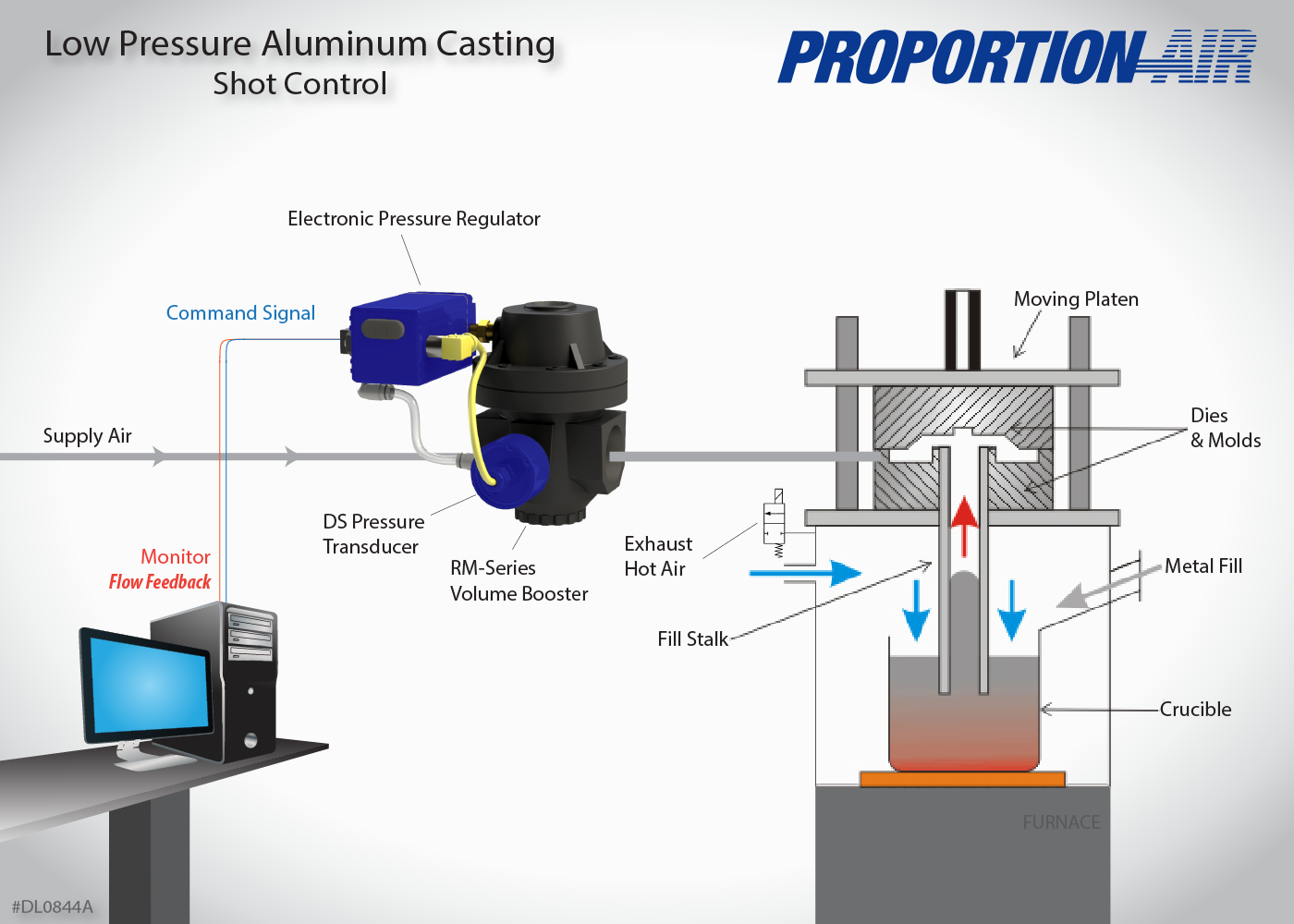
Perfecting low pressure aluminum casting for wheels requires accurate control of positive pressure to move molten aluminum into a mold quickly and achieve a finished product that has improved mechanical properties (higher density) over a gravity cast wheel. In the O.E.M. (Original Equipment Manufacturer) market, low pressure casting is the most common process approved for aluminum wheels. Historically, however, this process has been performed with sub-par pressure control components.
Proportion-Air has had many opportunities over the years to retro-fit casting machines with our American-made pressure controllers. This has provided us with extensive experience in perfecting a process that results in better quality, peace of mind and much less scrap for our customers. If you are interested in learning how we can help improve your low pressure casting process, continue reading and give us call.
3 Processes to Perfect
Shot Control
Temperature Control
Shot Control with Air Measurement
Low Pressure Aluminum Casting Shot Control
High resolution, low-pressure control is critical to good part manufacturing in low pressure aluminum casting. The QB2 and RM-Series regulator are the industry standard for shot control. Due to its closed-loop design, the QB2 is repeatable, even at pressures below 1 PSI. The unit follows a ramped command signal extremely well making it ideal for virtually any shot sequence. The QB2s analog monitor provides the PLC a signal from the downstream pressure transducer for data acquisition.
Common Shot Control Issues
Poor Resolution & Repeatability
Without great resolution, you cannot make the necessary (and extremely small) changes in pressure that is required during the shot control process.
Proportion-Air’s low-pressure casting controllers provide more than enough resolution to make the smallest changes required for consistent products.
Resolution is only valuable if it can be repeated. The majority of pressure controllers on the market do not even list a repeatability specification–maybe this says something?
In this application our controller will be repeatable to ±0.02% of full scale calibration.
Dog Leg Pressure Profile
Since most pressure controllers offer poor resolution and repeatability, casting machine PLC programmers struggle to get a linear and proportional pressure profile that begins just above zero PSI.
This ends up creating a “dog leg” in the pressure ramp profile that can cause molten metal to rise abruptly in the riser tube. This issue also almost always results in sub-par products.
Since Proportion-Air’s controller offers the same resolution, accuracy and repeatability throughout the entire range, the “dog leg” ramp in the process can be eliminated.
Furnace Leaks
Does your current pressure controller struggle to keep up with the pressure ramp over time?
As the seals of the furnace door start to wear and leak, the flow required becomes too much for the pressure controller to compensate for and bad parts begin to roll out.
The Proportion-Air pressure control assembly will naturally compensate for leaks – up to its flow capability. Our pressure controller comes with an analog monitor pressure signal that allows you to see pressure in the furnace during the entire shot process. This signal is commonly used for data acquisition. If pressure isn’t achieved during the shot sequence, leaks in the furnace may have exceeded the pressure controller’s flow capability and a bad part will be made. Pressure not achieved during the shot will allow you to know it’s time to replace your seal.
We can also add a flow monitor upstream of the shot controller to measure the flow of each shot. This provides direct feedback and perfect data acquisition pertaining to the life of the seal on the furnace door.
Instead of waiting until product is produced incorrectly you can be proactive and know when the seals need replaced. Compressed air is expensive so this can allow you to see leaks, fix them and save energy too.
Why use Proportion-Air as your shot controller?
- EXPERIENCE
We have 30+ years of experience in low pressure casting controls - RESPONSE TIME
Our dual-loop control is faster & more repeatable than traditional control methods - SIMPLICITY
a PID tuning loop is not required – Our controller is pre-set at the factory for easy installation - REPEATABILITY
Our controller is repeatable to ±0.02% f.s. – Example: 0-15 PSI range is repeatable to ±0.003 PSI - CUSTOMIZABLE
Our controller can be tailored to different furnace configurations, flows, accuracies and pressures
Low Pressure Aluminum Casting Temperature Control
Keeping parts cool during low pressure casting is always a challenge. The traditional method is to use a regulator to control pressure, but since the cooling process is under flow, controlling pressure always results in inconsistent and non-linear control. By controlling flow (instead of pressure), the exact amount of cooling air is always supplied and with Proportion-Air’s flow control package, this process is repeatable at ±0.25% of full scale calibration.
Common Temperature Control Issues
Poor Repeatability
Some low pressure casted parts have a mix of air and water cooling zones. Many manufacturers use pressure regulators to control cooling air. This is a mistake.
Certainly, air pressure adds a velocity that can be used to cool. However, it is not pressure itself that cools, but the flow of air.
That’s why we recommend controlling the flow (amount of molecules) into the cooling zones. Our closed-loop flow controller offers repeatability of ±0.25% for consistent and repeatable cooling.
It also has an analog monitor output signal showing the flow rate in the cooling zone for data acquisition to verify that the process flow was achieved and the part was cooled correctly every time.
Too Much Scrap!
Eliminate excess scrap by improving the efficiency and consistency of the entire process.
Low Pressure Aluminum Casting Shot Control with Air Measurement
The Proportion-Air QB2 and RM-series volume booster assembly provides excellent shot control with high resolution pressure control in low pressure aluminum casting.
But what if you could add predictive maintenance to your casting process?
By adding a F-series flow transducer upstream of the pressure control assembly, a real-time flow measurement can be obtained and monitored. As the flow in the process begins to increase, you know the seals on your furnace are beginning to wear. This predictive feature information allows you to run the process right up to failure without wasting product – because you know exactly how much flow is too much and you can easily stop and repair the seals when this flow level is reached.
Reach out to us to see how we can help you with your application.
Products used in this application:
-
QBX Industrial Electronic Pressure Regulator
$576.00 Select options This product has multiple variants. The options may be chosen on the product page -
RM Pilot-Operated Regulator
Read more